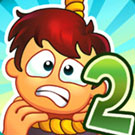
building a fiberglass boat from a mold
Some boat builders use a fiberglass chopper gun to help build a hull while others just say no. When working with a male mold you are building up laminate from the inside out; the outermost layer goes on last, and if you want the outside of your boat to look nice and shiny you must fair and polish the exterior surface afterward. Copyright 2023 Boating Basics Online. Allow the First Layer to Cure. Any tips on releasing a long mold from the plug? DIY Boat Building Plans Insert the knife into one corner of the backing board. Opting for a male mold would require you to lay over the fiberglass on its exterior surface. Building my 2.4 metre ( 8 feet ) dinghy hull mould from scratch Make sure to cover the flange with this glass. This article will guide you through two construction methods: build a fiberglass boat from a used watercraft or with a pre-made mold. To make a fiberglass boat, you have to prepare a mold for it due to its size. The inside and outside of fiberglass are strengthened and protected all at the same time by this substance. CLICK THE LINK TO ACCESS:http://snip.li/myboatplans===============================================In the manual you will find all about:How to Build a Plywood BoatHow to Build a Wooden FishingHow to Build a Wood boat Free PlansHow to Build a Wooden Boat from ScratchHow to Build a Wooden Speed BoatHow to Build a Small Wooden BoatHow to Build a Wooden SailboatHow to Build a Small BoatHow to Build a Fiberglass BoatBuild a Boat PlansStep by Step Build Fishing Boatboat building woodenwood boat buildingboat building planboat building blueprintswooden boat buildingplywood boat buildingboat building plywoodfibreglass boat buildingfree boat plansboat plans for freetimber boat plansmodel boat plansplywood boat plansboat plans plywoodsmall boat plansboat plans woodjon boat plansrow boat plansfishing boat plansduck boat plansaluminum boat plansrowing boat plansfree wooden boat planswooden boat plans freewooden boat plans for freesailing boat plansfan boat plansdrift boat planspower boat plansstitch and glue boat plansstitch \u0026 glue boat plansbuild boat plansbuild a boat plansboat plans and kitsboat plans download==================================https://en.wikipedia.org/wiki/Boat_building=================================================================https://youtu.be/LySXQPSrExMhttps://youtu.be/mvpIhJcPS9Ihttps://youtu.be/zkRkUwsqxKshttps://youtu.be/0wf9FO_hAEkhttps://youtu.be/mBsY8dX0ahYhttps://youtu.be/xm7fQD7DQ1Qhttps://youtu.be/iaJkXEQXyqkhttps://youtu.be/pFRf0-m6iPEhttps://youtu.be/HfXzzKsd6KYhttps://youtu.be/HIHuQchijYYhttps://youtu.be/Wg81wgWw9nshttps://youtu.be/8SfTlgKoH5shttps://youtu.be/5ccU99zGWx0https://youtu.be/hHFZr2o1pRkhttps://youtu.be/YJJuRTJsq1shttps://youtu.be/yhg9Vus-g3Qhttps://youtu.be/mTRDMXzS7Hkhttps://youtu.be/bgSOxkA0zzohttps://youtu.be/XhLgQ2Bva_whttps://youtu.be/sJB8lj0UFbM Let us look at the steps on how to apply fiberglass on your boat to make it more durable, long-lasting, and attractive. You cannot, for example, build a solid house of just mud or straw, but if you mix mud and straw together, you can build quite a strong house. Prepare the fiberglass cloth and cut it according to the shapes needed to cover your boat. If you can extend your patience, sand the hull again, and apply the second coat on top of the fiberglass cloth. boats.com is part of the Boats Group Network. In boats.com's Factory Fridays video series we tour boatings top manufacturing facilities across America. DIY Boat Building Plans Before the gel coat cures, apply a thin coat of epoxy resin. ("naturalWidth"in a&&"naturalHeight"in a))return{};for(var d=0;a=c[d];++d){var e=a.getAttribute("data-pagespeed-url-hash");e&&(! And then wait for around 30 minutes for the mixture to harden, and get ready to apply the toughened solution to the hull of your boat. But some shapes are still easier to form than others. When you build a fiberglass boat at home, you have the chance to customize it. You also need a half-inch or an inch allowance for the widest dimension when cutting the fiberglass. Most boaters depend on it as its tough and easy to repair with more advantages as it has low cost and maintenance. The existing part you want to use as a mold is actually the final object and not just a representation. [New and Used Jet Ski Prices], Kayaking in Ohio [Best 13 Places to Kayak in Ohio], Sit-In vs Sit-On Kayak [Difference Between Sit-On-Top vs Sit-In Kayaks], Clamping materials, hot glue, or whatever is available and appropriate. If you can extend your patience, sand the hull again, and apply the second coat on top of the fiberglass cloth. Remove the rails or lift stakes, keel, and other items that must not be integrated with fiberglass. The final resin coating must be evenly applied and smooth, and it needs to be thick enough that you can sand without creating damage to the fiberglass cloth. The curing time between each layer is not very critical. It's a good idea to check the measurements and to build a model from the free plans just to make sure you understand the process.One of the beauties of building yourself is that you don't have to buy everything at once, just get what you need when you can afford it. Share your thoughts with us in the comment section. It will also provide an extra layer of protection to the existing part that you are using as a plug. Do your research, or ask recommendation for renowned boat builders if you are unsure what brand to purchase. Use staples, tacks, or tape to attach them to the boat. Then, apply one layer of fiberglass cloth or mat over the entire surface of the existing part. Reinforce the corner between the mini-cell foam and the deck by laying strips of fiberglass mat against it and the gelcoat. As soon as the part is securely mounted on the backing board, fill any gaps or transitions between the board and the part so that the part and the fillers will act as one unit. You should also apply release wax several times. Theres nothing to worry about as all holes and even cracks in the boat are packed with resin. A prefabricated jig to form a hull is essential in this part. Boat construction always starts with a hull mold. It is important that you train your teams to be consistent when it comes to the technique of laying all the material. Learn more. The goal is to cover the deck with a 0.005 to 0.010 millimeter coat. Just lightly brush the entire hull with the help of a chip brush. Since the advent of fiberglass, however, boatbuilding has increasingly become an industrial process as opposed to a craft. How to Make a Fiberglass Boat Mold - Gone Outdoors There are various types of fiberglass: E-glass, S-glass, mat, Uni-Directional Fibers, Bi-Axial Fibers, and Tri-Axial Fibers. Speed - RC Gas Boats - 50 Deep V PLUG Build & Fiberglass Mold Construction - OK, haven't seen any threads on specifically fiberglass molding, or plug making. If you only intend to make yourself a boat, do not even consider making a mold. A classic full-keel shape with lots of deadrise and deep bilges, by comparison, is more problematic since it is often impossible to extract a deep, narrow keel from a one-part mold, no matter how carefully the mold is waxed beforehand. Give time for the gel coat to cure. Place three oz. A binding medium that is not structurally sound can be stiffened and made stronger by adding another more fibrous material. At this point, all the necessary applications are done. boats.com, 1221 Brickell Avenue, 23rd Floor, Miami, FL 33131, USA. A Gap In Understanding of Cored Construction. Bamboo, leather, paper, concrete. Anything under the core has no way of being seen because of the gel-coated surface on the other side. Youll see that it sits in a loose position, but whatsoever, you can get back to some areas for fixing to achieve the shape and appearance that you like. -Design Your Custom Boat With CAD Software \u0026 Building Guides. Apply Polyester Resin Over the First Coat. Now that you have the hull, you can proceed to build a fiberglass skiff to your liking. Then, put on disposable gloves and carefully install the fiberglass cloth. Place the fiberglass cloth on the resin coating Step 6. Building a mold out of existing boat. | SailNet Community Use the necessary fillers to cover any hole in your boat before you put fiberglass on the surface. Photo by Bavaria Boats. All you need to do is apply epoxy resin, glue one strand on the mold, and cover it with more epoxy. Builders like Sea-Ray, Ranger and Malibu use the chopper gun to lay down the first layer of fiberglass to avoid the pattern of woven roving from showing under the layer of gelcoat. Blend a fairing filler with epoxy following the manufacturers instructions. Many builders swear by it, while others eschew its use and instead, hand-lay layers of carefully cut sheets of woven roving fiberglass cloth down and wet it with resin. All Rights Reserved. In this case, a perfectly clean, highly polished two-piece mold to ensure no imperfections make it into the final composite. How to Build a Fiberglass Boat: The Ultimate Guide I get to travel, absorb knowledge about boating, and tackle all the issues when we sail into freedom! Boat Propeller Cavitation vs Ventilation: Whats the Difference? In this method, you have to place the fabric on the molds interior before wetting it out. Building a boat mold is one of the first steps in building a fiberglass boat. You can now use this mold to make a copy of the broken existing part. Some companies handle the issue of woven roving print-through differently. This Waverunner 65 / Euro 2000 was built in Cyprus using Bruce Roberts "Ezi-Build" fiberglass boat building methods as shown in our boat plans. FIBERGLASS BOATBUILDING: Creating a Laminate - boats.com If there is dry cloth that did not get wet under the core you will be able to see it with the camera because it is less dense and cools at a different rate, therefore, allowing you to know that there is an issue.. Operating a chopper gun is not a job a builder would give to a new-hire. When dry, pop out the plug and finish the inside surface of the mold. That is one way and probably the cheapest boat molds to be found. Afterward, grind the whole surface with an orbital sander. Use staples, tacks, or tape to attach them to the boat. Start Building the Fiberglass Mold. Then, we bag it, put it under vacuum and the resin is pulled through. You can search online for free plans or measure the mold and calculate the dimensions yourself. Many small start-up companies will purchase used boat molds then go into production making fiberglass boats. It may take time and effort when you commit to a DIY project. When you finish putting the fiberglass, youll find wet areas and some that are not. Molds themselves, of course, must also be created. H. Fiberglass boat. Spray a 0.5 millimeter thick layer of tooling gelcoat over the PVA mold release. For this to be possible, the molds working surface must first be coated with a waxy separating agent before the laminating begins. Since the early 1960s, fiberglass boat design and construction have become popular due to the materials outstanding strength, high stability, low production cost, and undemanding maintenance. The amount of necessary time varies as it affects the temperature. Above: From innovative marine propulsion systems and cutting-edge onboard technology, to the advanced physics of computerized hull design, boat builders share their fascinating stories and unique approaches to constructing and engineering a variety of watercraft in the Factory Friday video series from boats.com. Most of these machines are powered by hydraulic systems. In a bucket, mix the hardener and resin in the proportion recommended by the manufacturer. The core materials are especially applicable to sections of the plug or existing part that is generally flat and large. You may use plywood and some pieces of wood for this. When you buy via our links, we may earn a commission at no cost to you. In such a case, you need to use some form of the clamping system. In short, the process involves building a plug, which is an exact duplicate of the boat you want to build. More and more countries around the world are running out of timber and are building boats from fiberglass. Top 10 Choices for Boaters, Fiberglass Repair, Epoxy, Resin, and Help, Factory Fridays: Cigarette Racing Team's Boat Building Process - EP. The videos are in two parts, the first video shows the initial steps, and the second video shows the final steps leading to the release of the mold from the plug: Here are some useful tips on making fiberglass molds from existing parts. It does seem that something else might be better, though Forum posts represent the experience, opinion, and view of individual users. Although many modern boatbuilders eschew the use of wood, on high-end custom yachts like this Jarrett Bay, methods like cold molding are often considered superior to more modern techniques. We have foolproof methods for designing and building fiberglass molds to ensure the highest level of part quality no matter how high the production volume requirements are.
Cbbc Games Archive,
Why 6 Is The Coordination Number Of Fe3+,
Cruisin Classics Columbus Ohio Inventory,
Jimi Jamison Daughter,
Articles B