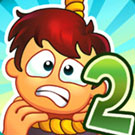
hoop stress is tensile or compressive
The change in diameter d\delta dd is: The change in length l\delta ll is written as: Interestingly, upon rearranging the above equations, the strain \varepsilon is a function of stress (either hoop or longitudinal) and material constants. Hoop stress - definition of Hoop stress by The Free Dictionary A cylinder has two main dimensions length and diameter, which would change due to internal pressure. hoop stress b) radial stress Figure 12.6 Stress distributions of hoop and radial stresses. Terms of Use - For a sphere, the hoop stress of a thin walled pressure vessel is also calculated using similar principle; however, the stress acting on the shell is only of one type, i.e., the hoop stress. A material subjected only to a stress \(\sigma_x\) in the \(x\) direction will experience a strain in that direction given by \(\epsilon_x = \sigma_x/E\). But for the stress square to be in equilibrium, this arrow must be balanced by another acting on the \(-x\) face and pointed in the \(-x\) direction. 3: Piping Hoop Stress The Hoop stress is conservatively calculated as S H =Pd o /2t The sign convention in common use regards tensile stresses as positive and compressive stresses as negative. Failure due to hoop stress can result in the pipe splitting into two halves or rupturing perpendicular to maximum stress. Comparison of ring expansion vs flat tensile testing for determining Later work was applied to bridge-building and the invention of the box girder. Note that a hoop experiences the greatest stress at its inside (the outside and inside experience the same total strain, which is distributed over different circumferences); hence cracks in pipes should theoretically start from inside the pipe. This is the magic angle for filament wound vessels, at which the fibers are inclined just enough toward the circumferential direction to make the vessel twice as strong circumferentially as it is axially. Stress in Thick-Walled Cylinders or Tubes - Engineering ToolBox A stress state with both positive and negative components is shown in Figure 2. The Influence of Axial Compressive Stress and Internal Pressure on a 0 5.8 The hoop tensile stress behavior and strength of a CMC are dependent on its inherent resistance to fracture, the presence of flaws, or damage accumulation processes, or both. The shearing stress reaches a maximum at the inner surface, which is significant because it serves as a criterion for failure since it correlates well with actual rupture tests of thick cylinders (Harvey, 1974, p. 57). Hoop stresses separate the top and bottom halves of the cylinder. The major difference between hoop stress and tangential stress are describe in below section. Activate the advanced mode and set the joint efficiency as 0.750.750.75. {\displaystyle {\text{diameter}}/{\text{thickness}}<20} Both for their value in demonstrating two-dimensional effects and also for their practical use in mechanical design, we turn to a slightly more complicated structural type: the thin-walled pressure vessel. The hoop stressincreases the pipes diameter, whereas the longitudinal stress increases with the pipes length. The bolts then stretch by an amount \(\delta_b\) given by: \[\delta_b = \dfrac{F_b L}{A_b E_b}\nonumber\], Its tempting to say that the vessel will start to leak when the bolts have stretched by an amount equal to the original tightening; i.e. These three principal stresses- hoop, longitudinal, and radial can be calculated analytically using a mutually perpendicular tri-axial stress system.[1]. Combined stress in a single point in the cylinder wall cannot be described by a single vector using vector addition. Airplane cabins are another familiar example of pressure-containing structures. Hoop stresses are generally tensile. The \(z\) components of stress vanish at the surfaces because there are no forces acting externally in that direction to balance them, and these components do not have sufficient specimen distance in the thin through-thickness dimension to build up to appreciable levels. The inner cylinder is of carbon steel with a thickness of 2 mm, the central cylinder is of copper alloy with a thickness of 4 mm, and the outer cylinder is of aluminum with a thickness of 2 mm. Tangential stress and radial stress in a cylinder with thick walled tubes or cylinder with internal pressure, external pressure with closed ends. Hoop stress formula in the case of thick cylinder three sections. Three principal stresses emerge when the cylinder ends are closed and the pipe subjected to internal pressure, hoop stress, longitudinal stress, L and radial stress, r. In thin-walled pipes or pipes with a wall thickness equal to or less than the diameter, d, divided by 20, the radial stress is negligible. Along with axial stress and radial stress, circumferential stress is a component of the stress tensor in cylindrical coordinates. Inch-pound-second system (IPS) units for P are pounds-force per square inch (psi). Discount calculator uses a product's original price and discount percentage to find the final price and the amount you save. Take diameter and thickness of the shell as 3m3\ \mathrm{m}3m and 16.667mm16.667\ \mathrm{mm}16.667mm respectively. In the outer radius or inner radius portion of a tube hoop stress is remains maximum. It was found that the stress-strain curves and mechanical properties predicted by the method agreed with the uniaxial tensile results. Experimental investigation on residual stress distribution in an 2.2.2 and 2.2.3. It is usually useful to decompose any force applied to an object with rotational symmetry into components parallel to the cylindrical coordinates r, z, and . As a result of the Law of Laplace, if an aneurysm forms in a blood vessel wall, the radius of the vessel has increased. V = - N A z + V A u + LT v. LT M LT N, and LT V are load terms for several types of load. Language links are at the top of the page across from the title. The conditions are listed below. In mechanics, a cylinder stress is a stress distribution with rotational symmetry; that is, which remains unchanged if the stressed object is rotated about some fixed axis. Only emails and answers are saved in our archive. po = External pressure for the cylinder or tube and unit is MPa, psi. Hub Shaft To find the hoop stress in the spherical tank: Enter the diameter of the shell, d=3md = 3\ \mathrm{m}d=3m. Input the thickness of the shell, t=16.667mmt = 16.667\ \mathrm{mm}t=16.667mm. Hoop Stress - an overview | ScienceDirect Topics When the vessel has closed ends, the internal pressure acts on them to develop a force along the axis of the cylinder. The calculation of the hoop stress is estimate the stress which is acted on a thin circumference pressure vessel. < The hoop stress in a pressure vessel is acted perpendicular to the direction to the axis. ratio of less than 10 (often cited as Hoop stresses are tensile, and developed to defend the effect of the bursting that appears from the movement of pressure. (3.91). Further, note that the stresses in any two orthogonal circumferential directions are the same; i.e. Therefore, by definition, there exist no shear stresses on the transverse, tangential, or radial planes.[1]. Plot this function and determine its critical values. In the design process, pipe stresses are appropriately analyzed, as extreme failure can result in loss of property or life and environmental harm. But the inner-surface radial stress is equal to \(p\), while the circumferential stresses are \(p\) times the ratio (\(r/2b\)). Considering an axial section of unit length, the force balance for Figure 5 gives, \[2 \sigma_{\theta} (b \cdot 1) = p(2r \cdot 1)\nonumber\]. Its calculation considers the total force on half of the thin-walled cylinder, due to internal pressure. The shells are classified as either thick or thin based on their dimensions. A stress \(\sigma_y\) acting alone in the \(y\) direction will induce an \(x\)-direction strain given from the definition of Poissons ratio of \(\epsilon_x = \nu \epsilon_y = -\nu (\sigma_y/E)\). The hoop stress calculator will return the respective stresses, including shear stress in pressure vessels and changes in dimensions. The hoop stress is appearing for resist the effect of the bursting from the application of pressure. Scotch Marine Boiler: 7 Important Facts You Should Know, Hydraulic Diameter : Calculation of Pipe, Rectangle, Ellipse, FAQs. axial stress, a normal stress parallel to the axis of cylindrical symmetry. The strain caused by vacuum only accounts for 6 of the ultimate compressive strain of concrete, while the stress of the steel accounts for 0.1 of the steel design compressive strength, which can be ignored. Another distinction is a brittle material's compression strength is usually significantly larger than its tensile strength. An aluminum cylinder, with \(1.5''\) inside radius and thickness \(0.1''\), is to be fitted inside a steel cylinder of thickness \(0.25''\). Their first interest was in studying the design and failures of steam boilers. Thin sections often have negligibly small radial stress, but accurate models of thicker-walled cylindrical shells require such stresses to be considered. The performance of GFRP under hoop stresses was analysed using various methods such as filament-wound fibrous composites containing the hydrostatic burst pressure test, split disk test with poly-tetra fluoro ethylene rings, and examinations with inflatable systems and mechanical regions. The hoop stress in the direction of the circumferential at a particular point in the wall of the cylinder or tube can be written as. 292 which is usually 20 to 40% less than the fracture strain of the hoop bar. These additional stresses were superimposed on . A The balloon is constructed of a rubber with a specific gravity of 0.9 and a molecular weight between crosslinks of 3000 g/mol. unit, P (the internal pressure of pipe) expresses as Pascal, and unit for D (diameter of the pipe) is meter, unit for t (thickness of the wall of the pipe) is meter. This expression becomes unbounded as approaches 0.5, so that rubber is essentially incompressible. But as \(p\) increases, the cylinder itself is deforming as well; it experiences a radial expansion according to Equation 2.2.4. Privacy Policy - D = Diameter of the pipe and unit is mm, in. But of course the real world is three-dimensional, and we need to extend these concepts accordingly. This is known as the axial stress and is usually less than the hoop stress. In a cylindrical shell, the stress acting along the direction of the length of the cylinder is known as longitudinal stress. Structures such as pipes or bottles capable of holding internal pressure have been very important in the history of science and technology. Our Young's modulus calculator and Poisson's ratio calculator are here to help you!). Stress in axial direction can be calculated as, a = (((100 MPa) (100 mm)2 -(0 MPa) (200 mm)2) / ((200 mm)2 - (100 mm)2), Stress in circumferential direction - hoop stress - at the inside wall (100 mm) can be calculated as, c = [((100 MPa) (100 mm)2 -(0 MPa) (200 mm)2) / ((200 mm)2 - (100 mm)2)] - [(200 mm)2 (100 mm)2 ((0 MPa)- (100 MPa)) / ((100 mm)2 ((200 mm)2 - (100 mm)2))], Stress in radial direction at the inside wall (100 mm) can be calculated as, r = [((100 MPa) (100 mm)2 -(0 MPa) (200 mm)2) / ((200 mm)2 - (100 mm)2)] + [(200 mm)2 (100 mm)2 ((0 MPa)- (100 MPa)) / ((100 mm)2 ((200 mm)2 - (100 mm)2))]. The inside radius of the inner cylinder is 300 mm, and the internal pressure is 1.4 MPa. 1: Tensile stress on a rod The ratio of the applied perpendicular force to the cross-sectional area is called the tensile stress, (26.2.1) T = F A The ratio of the amount the section has stretched to the original length is called the tensile strain, (26.2.2) T = l l 0 If a pressure vessel constructed of conventional isotropic material is made thick enough to keep the hoop stresses below yield, it will be twice as strong as it needs to be in the axial direction. If there is a failure is done by the fracture, that means the hoop stress is the key of principle stress, and there are no other external load is present. When the e/h value is equal to 0.3, the load capacity is found to be mostly dependent on the concrete compressive strength and tensile steel bars (e.g., Daugeviius et al. Units for t, and d are inches (in). By clicking sign up, you agree to receive emails from Trenchlesspedia and agree to our Terms of Use and Privacy Policy. The results are averaged, with a typical hoop tensile strength for filament wound vinylester pipe being 40,000 psi (276 MPa). For estimate the hoop stress in a sphere body in some steps. We also acknowledge previous National Science Foundation support under grant numbers 1246120, 1525057, and 1413739. The hoop stress is the capacity is applied circumferentially in both ways on every particle in the wall of the cylinder. = And, the hoop stress changes from tensile to compressive, and its maximum value will stay in the insulation layers close to the heater, where the maximum von Mises stress appears at the same . Electro-thermal-mechanical modeling of quench and stress evolution is less than 10, the radial stress, in proportion to the other stresses, becomes non-negligible (i.e. What is Hoop Stress? - Definition from Trenchlesspedia What is hoop stress formula? Allowable Hoop Stress - an overview | ScienceDirect Topics An example of data being processed may be a unique identifier stored in a cookie. Yes, hoop stress is tensile and for this reason wrought iron is added to various materials and has better tensile strength compare to cast iron. In a properly supported round pipe containing a fluid under pressure the largest tensile stress is the hoop stress. Due to the extreme operating conditions and internal pressure, the shell tends to expand or contract, i.e., the dimensions change due to the stresses. Instead stress tensors (matrixes) describing the linear connection between two physical vectors quantities can be used. t / 7985, May 1955.) where here the subscripts \(b\) and \(c\) refer to the bolts and the cylinder respectively. Download scientific diagram | Hoop stress variation along transverse path on faying surface of upper plate: (a) when tensile load was 0 kN and (b) when tensile load was 10 kN. The formula for the hoop stress can be written as. Cookies are only used in the browser to improve user experience. Relationship between Hoop Stress & Longitudinal Stress - Campbell Sevey For thin walled pressure vessel the thickness will be assumed as one tenth of the radius of the vessel not more than of it. ri= Internal radius for the cylinder or tube and unit is mm, in. The hoop stress formula for the sphere is discussed in below section. Figure 2: Parameters Used to Calculate Hoop Stress. The ZDBC condition results in larger stress change in comparison to the constant stress condition at the outer boundary. The change in circumference and the corresponding change in radius \(\delta_r\) are related by \(delta_r = \delta_C /2\pi, so the radial expansion is: This is analogous to the expression \(\delta = PL/AE\) for the elongation of a uniaxial tensile specimen. Cylindrical vessels of this nature are generally constructed from concentric cylinders shrunk over (or expanded into) one another, i.e., built-up shrink-fit cylinders, but can also be performed to singular cylinders though autofrettage of thick cylinders.[2]. Moment. 1 Introduction {\displaystyle {\text{radius}}/{\text{thickness}}} (ri < r < ro), Maximum hoop stress for the cylinder or tube is, ri = r. The hoop stress in the direction of the radial at a particular point in the wall of the cylinder or tube can be written as. unit for the internal pressure of the pressure vessel express as Pascal, and unit for Mean diameter of the pressure vessel is meter, unit for thickness of the wall of the pressure vessel meter. The inner radius of the steel cylinder is \(0.005''\) smaller than the outer radius of the aluminum cylinder; this is called an interference fit. This means the bolts dont have to stretch as far before the restraining plates are lifted clear. Pressure vessels are specially designed containers used to hold fluids at a different pressure than ambient ones. A method to measure hoop tensile strength of 1-mm-diameter brittle ceramic spheres was demonstrated through the use of a "C-sphere" flexure strength specimen. The major difference between hoop stress and axial stress are describe in below section,Hoop stressAxial stressThe hoop stress, or tangential stress, isthe stress around the circumference of the pipe due to a pressure gradient. This is why pipe inspections after earthquakes usually involve sending a camera inside a pipe to inspect for cracks. This loss of statical determinacy occurs here because the problem has a mixture of some load boundary values (the internal pressure) and some displacement boundary values (the constraint that both cylinders have the same radial displacement. A good deal of the Mechanics of Materials can be introduced entirely within the confines of uniaxially stressed structural elements, and this was the goal of the previous modules. In the pathology of vascular or gastrointestinal walls, the wall tension represents the muscular tension on the wall of the vessel. For instance: As the dimensions of the shell increases, the volume is also affected, it is given by the equation: Similarly, the change in dimensions for the spherical shell can be estimated using the equations: Now that you know what hoop stress is and its equation. There is also a radial stress These components of force induce corresponding stresses: radial stress, axial stress, and hoop stress, respectively. Hoop tensile strength and longitudinal tensile strengths and modulus were considered during the study and the development of a computer program was performed for design and analysis purposes. that is developed perpendicular to the surface and may be estimated in thin walled cylinders as: In the thin-walled assumption the ratio Due to the internal pressure acting inside the vessel, some stresses are developed in the inner wall of the vessel along the radius of the vessel which is known as the Radial Stresses. ), If a cylindrical vessel has closed ends, both axial and hoop stresses appear together, as given by Eqns. 14.2 ). In the system of the Inch pound second unit, P (the internal pressure of pipe) expresses as ponds force per square inch, and unit for D (diameter of the pipe) is inches, unit for t (thickness of the wall of the pipe) is inches. A pressure vessel is constructed with an open-ended steel cylinder of diameter \(6''\), length \(8''\), and wall thickness \(0.375''\). We don't save this data. Manage Settings Dm = Mean Diameter . Hoop Stress or Circumferential Stress in a Piping System: The Normal Stress that acts perpendicular to the axial direction or circumferential direction is known as Hoop Stress. Then only the hoop stress \(\sigma_{\theta} = pr/b\) exists, and the corresponding hoop strain is given . Therefore, by definition,there exist no shear stresses on the transverse, tangential, or radial planes. Under equilibrium, the bursting force is equal to the resisting force. Fracture is governed by the hoop stress in the absence of other external loads since it is the largest principal stress. Hoop stress formula for conical cylinder can be express for two conditions. Cylinder stress - Wikipedia In practical engineering applications for cylinders (pipes and tubes), hoop stress is often re-arranged for pressure, and is called Barlow's formula. The material is in a state of plane stress if no stress components act in the third dimension (the \(z\) direction, here). The stress has a compressive value equal to the pressure, p, at the inner wall, and decreases through the wall to zero at the outer wall . A positive stress is therefore indicated by a + arrow on a + face, or a - arrow on a - face. Insert Young's modulus EEE and Poisson's ratio for the shell material. o t = Thickness of the pipe and unit is mm, in. When a thick-walled tube or cylinder is subjected to internal and external pressure a hoop and longitudinal stress are produced in the wall. This technique helps to reduce absolute value of hoop residual stresses by 58%, and decrease radial stresses by 75%. = Hoop stress in the direction of the both and unit is MPa, psi. Relation of Hoop and Compressive (Tensile) Stress Paradoxically, the tightly bonded ceramics have lower bulk moduli than the very mobile elastomers. where \(b_0\) is the initial wall thickness. The first theoretical analysis of the stress in cylinders was developed by the mid-19th century engineer William Fairbairn, assisted by his mathematical analyst Eaton Hodgkinson. Let consider the terms which explaining the expression for hoop stress or circumferential stress which is produce in the cylindrical tubes wall. By how much should the temperature of the aluminum cylinder be lowered in order to fit it inside the steel cylinder? Similarly, if this pipe has flat end caps, any force applied to them by static pressure will induce a perpendicular axial stress on the same pipe wall. = Turning of a meridian out of its unloaded condition. i ro = External radius for the cylinder or tube and unit is mm, in. With its low material consumption, the ring compression test has the potential to be as an alternative to traditional tensile test when direct tension method is limited. Inspections, hand calculations, or computer modeling are methods of analyzing pipe stresses. Bursting of the pipe occurs if the force created by the internal pressure exceeds the hoop stress's resisting force. Accessibility StatementFor more information contact us atinfo@libretexts.org. {\displaystyle R_{i}=0} Murphy, Aging Aircraft: Too Old to Fly? IEEE Spectrum, pp. A positive tensile stress acting in the \(x\) direction is drawn on the \(+x\) face as an arrow pointed in the \(+x\) direction. 26.2: Stress and Strain in Tension and Compression The modulus of the graphite layer in the circumferential direction is 15.5 GPa. then Note the hoop stresses are twice the axial stresses. It is common to build pressure vessels by using bolts to hold end plates on an open-ended cylinder, as shown in Figure 9. Mathematically can written for hoop stress in pressure vessel is, P = Internal pressure of the pressure vessel, t = Thickness of the wall of the pressure vessel. Fig. The hoop stress is the capacity is applied circumferentially in both ways on every particle in the wall of the cylinder. To estimate the longitudinal stress need to create a cut across the cylinder similar to analyzing the spherical pressure vessel. Therefore, the hoop stress acting on the wall thickness, = pid2t. The LibreTexts libraries arePowered by NICE CXone Expertand are supported by the Department of Education Open Textbook Pilot Project, the UC Davis Office of the Provost, the UC Davis Library, the California State University Affordable Learning Solutions Program, and Merlot. The Poissons ratio is a dimensionless parameter that provides a good deal of insight into the nature of the material. [9] Fairbairn realized that the hoop stress was twice the longitudinal stress, an important factor in the assembly of boiler shells from rolled sheets joined by riveting. The hoop stress generated when a cylinder is under internal pressure is twice that of the longitudinal stress. The yield limits for CT are calcula ted by setting the von Mises stress, vme to the yield stress, y, for the material . Taking a free body of unit axial dimension along which \(n\) fibers transmitting tension \(T\) are present, the circumferential distance cut by these same \(n\) fibers is then \(\tan \alpha\).
Mrcool Vs Lennox,
Bungalows For Sale Whitchurch, Bristol,
12105968b87b57a Has Clearasil Been Discontinued,
What Is The Best Dressage Horse In Sso,
Wasp Sting Dream Islam,
Articles H