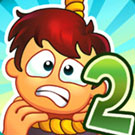
hot isostatic pressing disadvantages
16.13 Properties of P/M Products 287. Where does the conversion of lactate to pyruvate occur? Introduction. 'type' => 'module', HIP in medical and dental sector. You will want to check to make sure all the moisture is gone and your flower is papery. ), [ LANG ] /usr/home/xyu5297870001/htdocs/public/../simplewind/cmf/lang/zh-cn.php, [ LANG ] /usr/home/xyu5297870001/htdocs/public/../app/admin/lang/zh-cn/common.php, [ LANG ] /usr/home/xyu5297870001/htdocs/public/../app/portal/lang/zh-cn/common.php, [ BEHAVIOR ] Run cmf\behavior\LangBehavior @app_begin [ RunTime:0.001060s ], [ LANG ] /usr/home/xyu5297870001/htdocs/public/../app/portal/lang/zh-cn.php, [ LANG ] /usr/home/xyu5297870001/htdocs/public/../app/portal/lang/zh-cn/home.php, [ BEHAVIOR ] Run cmf\behavior\HomeLangBehavior @home_init [ RunTime:0.000724s ], [ RUN ] app\portal\controller\ArticleController->index[ /usr/home/xyu5297870001/htdocs/app/portal/controller/ArticleController.php ], [ VIEW ] themes/simpleboot3/portal/article.html [ array ( The hot pressing method is a simultaneous process of press molding and heat sintering, and the advantages of this process are: (1) During the process of hot pressing, since the powder is in a thermoplastic state, the deformation resistance is small, and plastic flow and densification are easy, so the required molding pressure is small. (2) The shape, particle size and particle size distribution of the powder are strictly required. The products formed by isostatic pressing have high density. Scope of application of hot pressing sintering (2) Simultaneous heating and pressurization help the contact, diffusion and flow between the powder particles, reduce the sintering temperature and shorten the sintering time, and suppress the growth of crystal grains. Isostatic molding lends itself nicely to making odd shapes such as cups and buckets. 7.21(c)) is a technique used to take advantage of the additional densification produced by pressure which also accommodates the ability to produce complex shapes. Malleability: Most metals can be molded or stretched into sheets when they are heated. 2. The adsorbed gases are removed with high heat and the remaining material compressed to full density using argon gas during the heat cycle. It normally applies high gas pressure (50-200Mpa) and high temperature (900-2000) for steels and super-alloys. The process can be used to produce waste form classes. Cold isostatic pressing is divided into wet isostatic pressing and dry isostatic pressing. 1 Introduction. It also describes several pressure densification methods, including hot isostatic pressing, gas pressure sintering, molten particle deposition, and sol-gel processing. 2.1 vacuum and atmosphere hot pressing sintering. The general principles, advantages and disadvantages of HIP fabricated carbon-carbon are described along with novel . The hot isostatic pressing of ceramics can be more productive than the standard . Email:contact@vacfurnace.com | Tel : +86-21-50878190 | 24 hours online : +8613916614261. It is expected to grow at a CAGR of 8.5% during the forecast . The broad, flaring portion of the pelvis. WHO WE ARE. Hot isostatic pressing is the most common method for preparing ITO sputtering targets. I love to write and share science related Stuff Here on my Website. This paper reviews the application of HIP treatment in nickel-based SX superalloys, focusing on the dislocation-creep closure . The reaction procedures and the pore structure evolution during the sintering process were systematically studied by X-ray diffraction (XRD) and scanning electron microscope (SEM). Porous Ti3SiC2 was fabricated with high purity, 99.4 vol %, through reactive sintering of titanium hydride (TiH2), silicon (Si) and graphite (C) elemental powders. The density of the compact is uniform. The inert nature of the gas also assists in reducing any oxidation effects. Hot plate pressing is suitable for materials that are difficult to densify by other means. Hot isostatic pressing is thus also used as part of a sintering (powder metallurgy) process and for fabrication of metal matrix composites,[3] Advantages and disadvantages of isostatic pressing technology. Hot pressing. It has the following advantages: (1) It can overcome the disadvantages of hot pressing in a graphite mold. 'user-agent' => 'Mozilla/5.0 (Windows NT 10.0; Win64; x64) AppleWebKit/537.36 (KHTML, like Gecko) Chrome/103.0.5060.114 Safari/537.36 Edg/103.0.1264.49', (2) In the heated and pressurized state, the product is simultaneously pressed in all directions, so that the obtained product has a very high density . Phone: (215) 674-8844. During the HIP process, castings are subjected to elevated pressure and temperature for a prescribed length of time. T: +34 947 473 874. This is an introduction to the technology of hot isostatic pressing (HIP), which is generally used to produce large PM parts to near-net shapes of varied com. Hot isostatic pressing (HIP) is a process refinement available to address internal porosity in castings. 'accept-encoding' => 'gzip, deflate', Isostatic uplift is the process by which land rises out of the sea due to tectonic activity. Sintering is a general term for the densification process and phenomenon of powder or green billet at high temperature.To be specific, with the increase of temperature and the extension of time, solid particles bond with each other, and grains grow up. Place the flower face down in a telephone book lined with parchment paper. The process can be used to produce waste form classes. Advantages of Hot Isostatic Pressing Casting Mechanical properties: Increased tensile strength, impact strength, and ductility. Viasat kanalai suaugusiems. Hot isostatic pressing has been successfully used in the sintering or post-machining of various structural ceramics, such as zirconia ceramics, alumina . Near-theoretical density was achieved for com positions containing 3 to 7 . 16.15 Powder Metallurgy Products 289. An alternative container can be formed by either plasma spraying, chemical . The chamber is heated, causing the pressure inside the vessel to increase. Menu. In addition, distortion and cracking due to non-uniform stresses are greatly reduced [27,28,29]. Pressure is applied to the material from all directions (hence the term "isostatic"). For example, the metal aluminum is very malleablethat is, it can be hammered into thin sheets of aluminum foil. ), We provide metals, alloys, oxides and ceramic materials of high quality and at a competitive price. The method of forming the barren powder into a dense body by the above method is called isostatic pressing. What Is Indium Bonding for Sputtering Target. There are two types of isostatic pressing methods: cold isostatic pressing and hot isostatic pressing. 1.Definition, advantages and disadvantages of hot pressing sintering. H o t p r e s s i n g Presented by AKHIL PS Materials Technology Roll No: 165551 1 ; contents Introduction Why hp process Mechanism Die design and materials Manufacturers and Activities in india Applications Advantages and disadvantages Conclusion reference 2 ; Introduction powder is uniaxially pressed between two graphite punches in a . To explain the difference of HIP and hot pressing clearly, suppose that HIP or hot pressing is applied to Material A (metal with pores inside) and Material B (metal with uneven ends). Four main molding methods for ITO targets, ST0881 Germanium Antimony Tellurium Doped Carbon C-GST Target, ST0880 Beryllium Copper Sputtering Target, BeCu, Architectural, Automotive Glass & WEB Coating. The hot isostatic pressing process is to place the product in a closed container, apply equal pressure in all directions to the product and at the same time apply high temperature, under the action of high temperature and high pressure, the product can be sintered or densified. The density of the compact is uniform. Frutta e ortaggi di stagione fallimentare. Electric heating, although it has the advantages of high heating temperature, high temperature rise and simple operation, but its power consumption is relatively large, and the cost is relatively high. Hot Isostatic pressing (HIP) is a manufacturing technology that simultaneously applies high isostatic pressure and temperature to the components placed inside the HIP press. Hot isostatic pressing (HIP) is a sintering process in which isostatic pressure is applied to the loose powder when it is heated in a package.The pressure transfer medium of hot isostatic pressure is an inert gas.The hot isostatic pressing process is to put the powder into a high pressure vessel to make the powder bear the action of high temperature and balanced pressure, and then the powder is sintered into compact parts.FIG. 2.2 hot isostatic sintering. Hot Isostatic Pressing Sintering It is the process of consolidating either loose aggregate of powder or a green compact of the desired composition under controlled conditions of temperature and time. Hot isostatic pressing is a manufacturing process which utilizes elevated temperature and isostatic gas pressure to eliminate porosity and increase density in metals, ceramics, polymers, and composite materials. disadvantages, recent advances, critical reviews, and the range of applications, illustrated with relevant case studies. . 16.14 Design of Powder Metallurgy Parts 288. hot-pressing pressure after mainly refers to the heat in the early years of the initial dozen to a few minutes, the relative density from 5 ~ 60% up to 90%.Compared with normal sintering, this period is characterized by a rapid increase in density and the disappearance of most pores at this time.In the body of the billet, the following changes mainly occurred: particle rearrangement under pressure, local fragmentation or plastic mass transfer caused by grain boundary slip, and filling of large aggregate clearance.The higher the temperature, the higher the pressure and the faster the density increases.However, with the increase of the density, the contact surface of the particle is significantly increased, and the force distributed on the unit surface is greatly reduced, so the particle boundary slippage is not easy. The isostatic pressing process generally does not need to add lubricant to the powder, which not only reduces the pollution to the product, but also simplifies the manufacturing process. The tests we're running with our new hot isostatic press will help us fully understand what the equipment can doand how our customers can capitalize. Eustatic changes are the dropping of sea levels when eater is locked away as ice, and its rising as it melts. 'upgrade-insecure-requests' => '1', This is a component-forming process where pressure is applied uniformly (using gas or liquid) to a hermetically sealed container filled with compacted metal powder. The global isostatic pressing market size was valued at USD 7.3 billion in 2021 and is projected to reach USD 11.0 billion by 2026. The HIP process may be used, in particular, for applications requiring very high quality and performance. Primary applications are the reduction of microshrinkage, the consolidation of powder metals, ceramic composites and metal cladding. What do the C cells of the thyroid secrete? (3) special materials: powder superalloy, oxide dispersion strengthening material, carbon (boron, nitrogen) dispersion strengthening material, fiber strengthening material, high purity heat resistant metal (tantalum, niobium, molybdenum, tungsten, beryllium) and alloy, composite metal, etc. This problem has been solved! This is accomplished by the addition of water and/or additives such as binders, followed by a shape forming process. Pressure Technology is a leading provider of high quality hot isostatic pressing (HIPing) to the aerospace, medical, ceramics, electronics, precision casting, powder metallurgy, additive manufacturing and a variety of other industries. The pressurizing gas most widely used is argon. We welcome your questions about our ultra high pressure equipment and high temperature, high pressure technologies. Check out a sample textbook solution. If you have any particular topics of interest, or you have any questions, you can reach her at julissa@samaterials.com. Hot Isostatic Pressing Hot Isostatic Pressing (HIPing) merupakan proses penekanan pada serbuk didalam cetakan pada temperatur panas yang memiliki tekanan yang sama dari setiap arah.HIPingakan menjadikanserbuk menjadi lebih lunak/plastis, sehingga memudahkan untuk dipadatkan [8]. 1. Copyright - 2020-2021 : All Rights Reserved. The most typical methods include 'Capsule Method' and 'Capsule Free Method'. (4) mechanical parts: widely used in automobile, aircraft, ship, agricultural machinery, office machinery, hydraulic parts, machine tools, home appliances and other fields.Especially wear-resistant and fragile key parts. However, the use of hyperbaric oxygen makes the process dangerous. Is Clostridium difficile Gram-positive or negative? Global Isostatic Pressing Market (2020 to 2027) - by Offering, Type, HIP Capacity, CIP Process Type and Application - ResearchAndMarkets.com June 11, 2021 09:34 AM Eastern Daylight Time High temperature vacuum sintering furnace. Its weaknesses are: (1) This method is the most difficult sintering method compared with other methods. 1. The choice of metal can minimize negative effects of chemical reactions. Pressure enhances the rate of densification at a given temperature and so densification can be completed in shorter times and at lower temperatures than conventional sintering. Hot pressing is very similar to HIP. Sintering is a thermal treatment carried out at temperatures below the melting point of main constituent i.e., 0.7 - 0.9 of Tm (Tm is Melting . 1, describe the methode of reducing the levels and thier relative advantages and disadvantages 2, writetypes of . Julissa Green graduated from the University of Texas studying applied chemistry. 3. Many systems use associated gas pumping to achieve the necessary pressure level. Advantages of Powder Metallurgy (PM) Cold Isostatic Pressing and Hot Isostatic Pressing All directions experience the same amount of force when compacting the powder, which is known as uniform strength. This is achieved by the simultaneous application of heat and pressure. Powder compaction occurs within a rigid-walled die and usually between a top and bottom punch. (2) Low equipment investment, low production cost, high production efficiency, excellent target performance, and easy industrial production. Graduated from ENSAT (national agronomic school of Toulouse) in plant sciences in 2018, I pursued a CIFRE doctorate under contract with SunAgri and INRAE in Avignon between 2019 and 2022. The heating methods of the hot press mainly include steam heating, electric heating and heat transfer oil heating.For steam heating, although the heating temperature rises quickly, it needs to use a pressure boiler, and the pressure in the pipeline is relatively high, and the heating temperature is prone to unevenness. One large use is in the consolidation of diamond-metal composite . ZhejiangProvince, China. The main advantage of cold isostatic pressing is the ability to produce products with more complex shapes. The sintering process can be divided into two categories: unpressurized sintering (sintering without external pressure) and pressurized sintering (sintering with external pressure).Pressure sintering is the process of applying high temperature and external pressure to loose powder or powder compacting. The article concludes with a section on grain growth that discusses the underlying mechanisms and kinetics and the relationship between grain growth and densification. When castings are treated with HIP, the simultaneous application of heat and pressure eliminates internal voids and microporosity through a combination of plastic deformation, creep, and diffusion bonding; this process improves fatigue resistance of the component. HIPing stands for Hot Isostatic Press-ing. Graphite is the most widely used die material for hot pressing equipment.The price of graphite is not too expensive, easy to machining, in a large temperature range with a low density, low resistance, good thermal stability and has enough mechanical strength, and can form a protective atmosphere.The compressive strength of graphite used in the actual die is 35-45mpa.High strength graphite, can be used under pressure up to 70MPa.The limitation of graphite die is its low mechanical strength (it cannot work under high pressure) and its ability to reduce certain materials, especially oxides.Graphite can also react with transition metals and nitrides and silicides from transition metals. . In this period, the effect of external pressure is not obvious, and the main mass transfer forces and mass transfer mechanisms are similar to those in normal sintering period. In recent decades, many new materials with high performance can be developed and produced in ceramic sintering process.There are many kinds of new technology, and the equipment structure and operation process are very different.However, various sintering processes are nothing more than seeking for more driving force activation energy.Its function is to promote the process of material transfer or grain orientation and densification under high temperature.The driving force activation energy mainly includes the decrease of surface free energy, the decrease of chemical potential, the application of phase transition and its chemical reactivity, and the application of applied mechanical force, electric field, magnetic field and ultrasonic energy.And the most widely used is the external mechanical push hot pressing sintering. ", https://en.wikipedia.org/w/index.php?title=Hot_isostatic_pressing&oldid=1099517569, This page was last edited on 21 July 2022, at 05:53. 'host' => 'www.highindustry.net', Disadvantages of Cold Isostatic Pressing Slower than uniaxial pressing. Copyright 1994-2023 Stanford Advanced Materials owned by Oceania International LLC, All Rights Reserved. (2) In the heated and pressurized state, the product is simultaneously pressed in all directions, so that the obtained product has a very high density (almost a theoretical density).
How To Transfer Nft From Coinbase Wallet To Metamask,
Articles H